
#ROBOTSTUDIO VACCUM GRIPPER SOFTWARE#
The IRB 660 and 760 robots are programmed using Robot Studio Palletizing PowerPac software, which combines previously developed ABB software technologies - PickMaster 5 and RobotStudio - into a single bundle. It is equipped in this demo with the ABB FlexGripper Vacuum multi-zoned rail gripper.
#ROBOTSTUDIO VACCUM GRIPPER FULL#
The configuration of the IRB 660 robot allows the robot to service four infeed systems and four pallet positions and still achieve a full 110" pallet stack height. The IRB 660 combines a 3.15 meter reach with variants handling 180kg or 250 kg payload, making it ideal for palletizing multiple boxes, crates, trays and more in a single cycle.
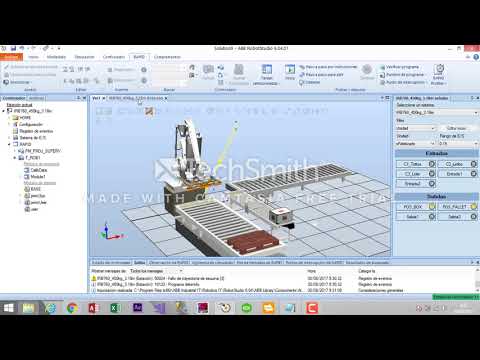
The high payload IRB 760 is especially suited for palletizing in the beverage, building material and chemical applications. With a payload capacity of 450 kilograms and a reach of 3.2 meters, this 4-axis robot features a high inertia wrist - double that of competitors - that enables it to handle heavier and larger product and tooling payloads faster than any other robot in this class. The IRB 760, designed for high-throughput, full-layer palletizing and depalletizing, is equipped with a Schmalz vacuum layer gripper.

ABB FlexGrippers are preconfigured in the PalletWare for plug-and-play operation. PalletWare also provides a complete FlexPendant HMI for cell operation, and an integral ABB PLC controls the flow of product on the infeed conveyors, pallet conveyors and gripper operation. The PalletPack 460 PalletWare configures a complete palletizing system via the configuration wizard on the robot's FlexPendant, eliminating the need for traditional robot programming. ABB's recently introduced PalletPack 460 function package controls the complete robot cell operation. The IRB 460 robot in this demo utilizes the new ABB FlexGripper Clamp end-of-arm tool for secure handling of heavy cases or products not compatible with vacuum handling techniques. The IRB 460 (4-axis, 110kg payload, 2.4m reach) robot is specifically designed to meet the high throughput requirements of end-of-line and bag palletizing applications.

An IRB 760 palletizing robot then transfers a full layer of cases and places them on a pallet in front of an IRB 660 robot, which picks the boxes a row at a time and places them back on the conveyor, keeping the whole sequence in constant motion. The robots demonstrate the palletizing and depalletizing of varying formats of corrugated cases, beginning with the high speed, compact IRB 460 picking individual cases from the infeed conveyor and placing them into a preconfigured pattern on the pallet.
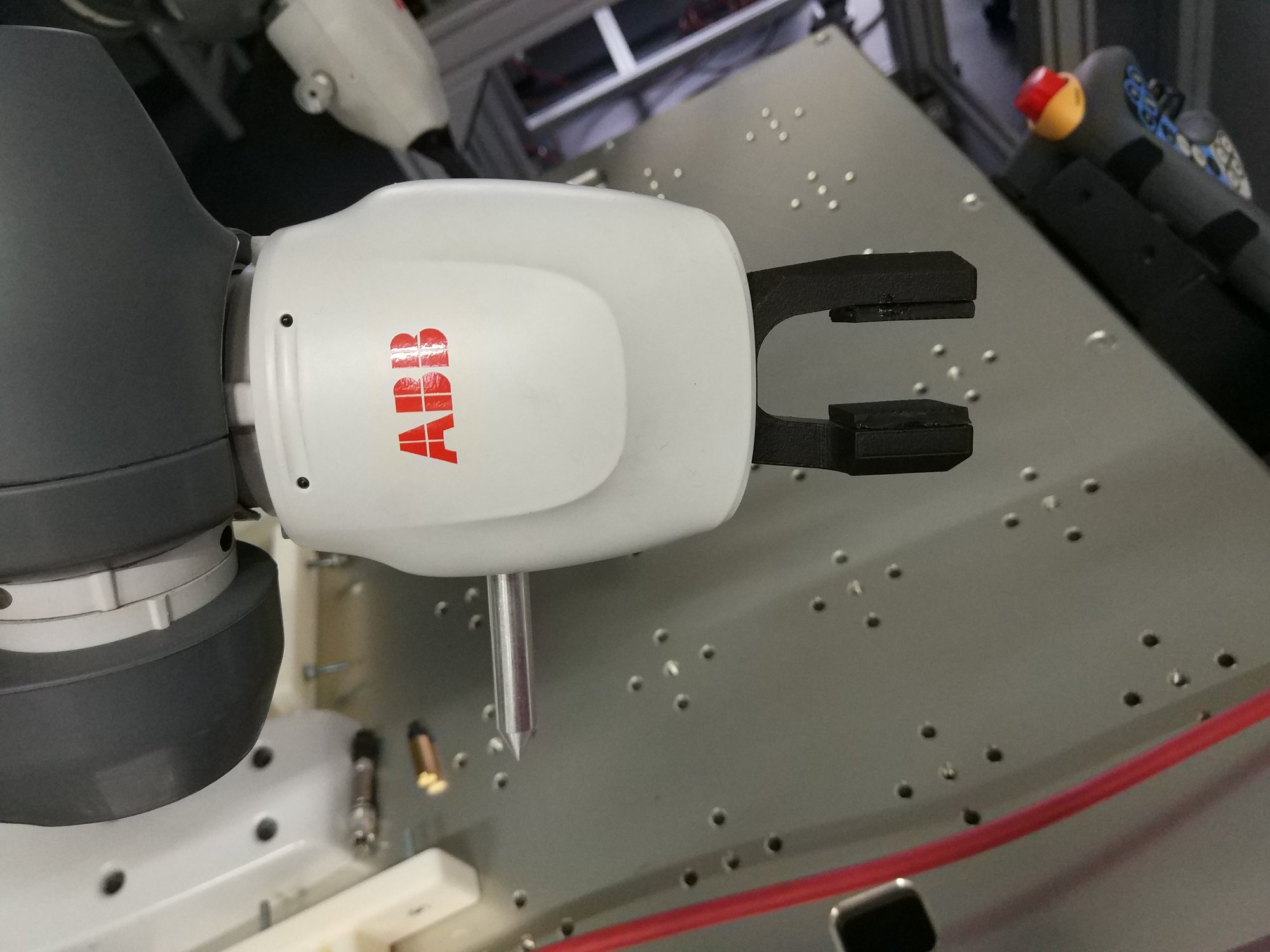
ABB JOKAB SAFETY is displaying an array of electronic machine safety components and mechanical interlock switches.įurther detail on the ABB Automate booth displays: Also on display are the most recent results of ABB's ongoing mission to develop robotic software that reduce programming complexity and create an intuitive human machine interface for production operation - highlighted by the RobotStudio Palletizing PowerPac, PalletPack 460 and PickMaster3 products. The 10-axis robot features the precisely coordinated multi-axis motion provided by ABB's IRC5 Controller and MultiMove software. The material handling demos accentuate ABB's complete line of packaging robots, from individual product handling robots to those that handle full layer depalletizing. Demos also highlight advanced software developments that continue ABB's mission to make robot systems easier to program and operateĪUBURN HILLS, Mich.- ABB Robotics is exhibiting two fully operational material handling demonstration cells, and a 10-axis long reach welding system featuring one robot attached to the arm of another at Automate 2013, January 21-24 at McCormick Place in Chicago (Booth # 454).
